Introducción
A medida que el tamaño de los motores cohete que voy construyendo
se fue incrementando, y también el de los cohetes, apareció
la necesidad de contar con piezas de aleación liviana que no son
obtenibles en el mercado local o en tamaños y formatos que implicaban
elevados costos por tener que partir de piezas grandes (alto costo) y
luego requerir mucho mecanizado (alto costo también). Con un horno
de este tipo se puede fundir y hacer las piezas con las aleaciones que
uno requiera. Seguramente no se obtendrá la pieza "ideal"
pero si algo bastante cercano.
También un horno de ese tipo permite obtener aleaciones como el
Magnalium, que es una aleación de aluminio y magnesio. Otro de
los usos es calcinar los restos de sales y lodos que me van quedando de
los procesos de preparación de Perclorato de Amonio y así
reducir el peso del material para la disposición final.
Para construirlos se uso materiales reciclados o sobrantes de otros trabajos
que se pudieron conseguir a precios reducidos.
Construcción
Se brindan los lineamientos generales que utilicé
para armar este horno. El punto de partida
fue decidir que tamaño de crisol se requiere y adquirirlo.
Luego hice un bosquejo del horno y definí el diseño. Los
etapas constructivas y materiales utilizados se brindan en una serie de
imágenes como guía constructiva.
IMPORTANTE: utilice los elementos de seguridad requeridos
para los trabajos que realice, como ser antiparras de seguridad, máscara
antipolvo (el corte de los ladrillos aislantes genera mucho polvillo!)
guantes, protectores auditivos, etc. |
Se preparó un video sobre este horno que se puede
ver en: http://www.youtube.com/watch?v=LQKVH_BZxCo
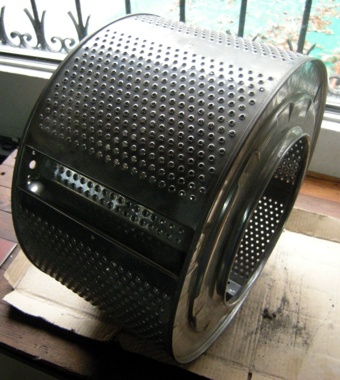 |
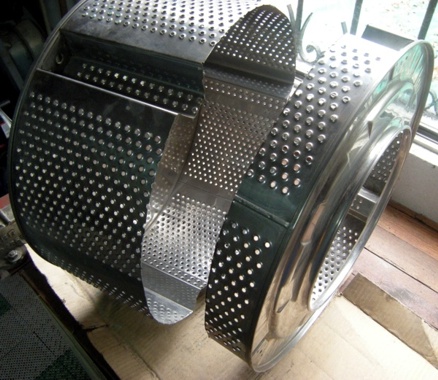 |
Fig nº 1.- Primer paso: conseguir un tambor
de lavarropas de desguace. Limpiarlo bien. Son de acero inoxidable
y bastante robustos para el uso que se le va a dar. |
Fig nº 2.- Segundo paso: se lo corta al tambor
con una amoladora y se le aplana un poco el fondo con un martillo.
Eliminar aristas agudas del corte. |
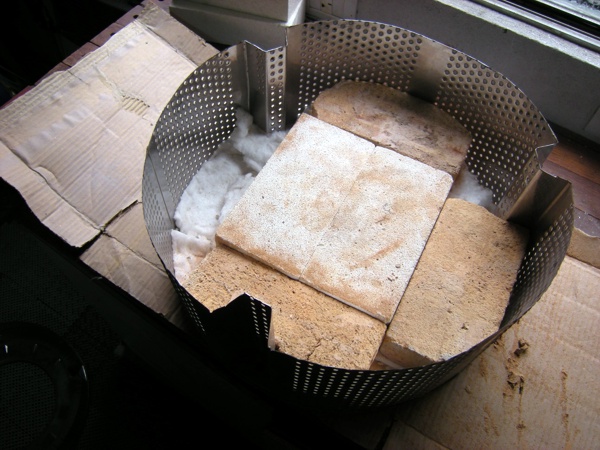 |
Fig nº 3.- Tercer paso: Se pone una capa de
fibra cerámica de unos 12 mm para uniformizar el nivel del
fondo y sobre ello se dispone una capa de ladrillos aislantes. Se
asegura que estén a nivel. Estos ladrillos aislantes son recuperados
durante el desarme de hornos industriales. |
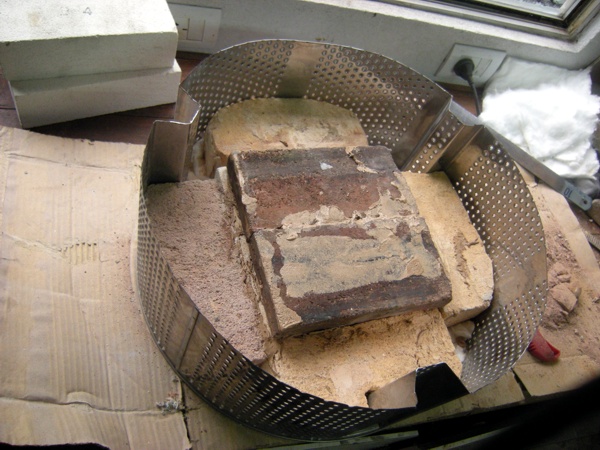 |
Fig nº 4.- Cuarto paso: Se completa la base
y se unen los ladrillos con cemento refractario. Se ponen en el centro
dos tejuelas de ladrillos refractario que van a conformar la base
de la cámara del horno. |
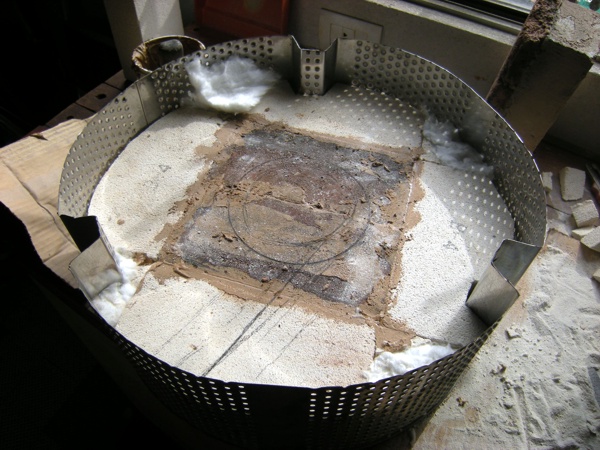 |
Fig nº 5.- Quinto paso: Se completan los laterales
con ladrillos refractarios y manta cerámica. Todos los ladrillos
van unidos con cemento refractario con espesor de 1 a 2 mm. Se marca
con lápiz la posición del crisol y el perímetro
interno de la cámara del horno. Se marca la entrada tangencial
de la llama del quemador y luego se corta la chapa para permitir la
ubicación de la entrada del quemador.. |
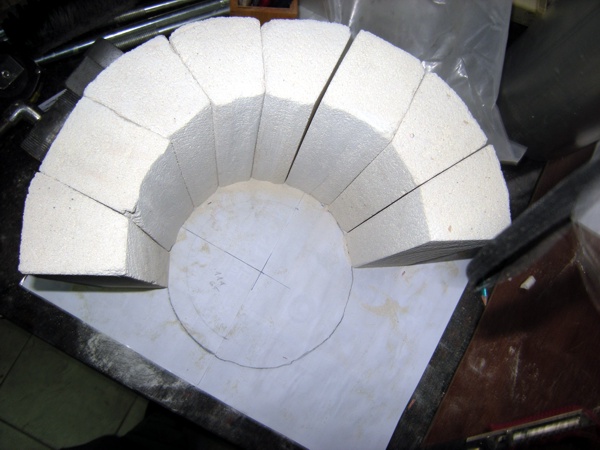 |
Fig nº 6.- Sexto paso: Se cortan por la mitad
(en forma oblicua y recta segun el caso) los ladrillos aislantes y
se los va conformando para hacer la cámara del horno. Luego
se los va ubicando sobre una plantilla de papel. Una vez que se completado
el circulo se los va poniendo en la base del horno y uniéndolos
con cemento refractario. Se deja un canal para el ingreso de la llama
del quemador ahí donde se lo había marcado. |
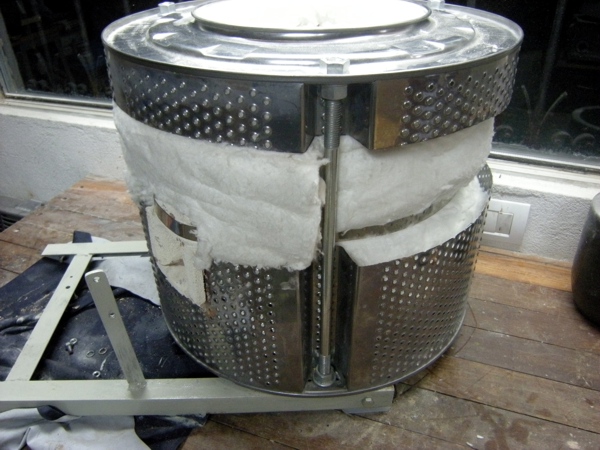 |
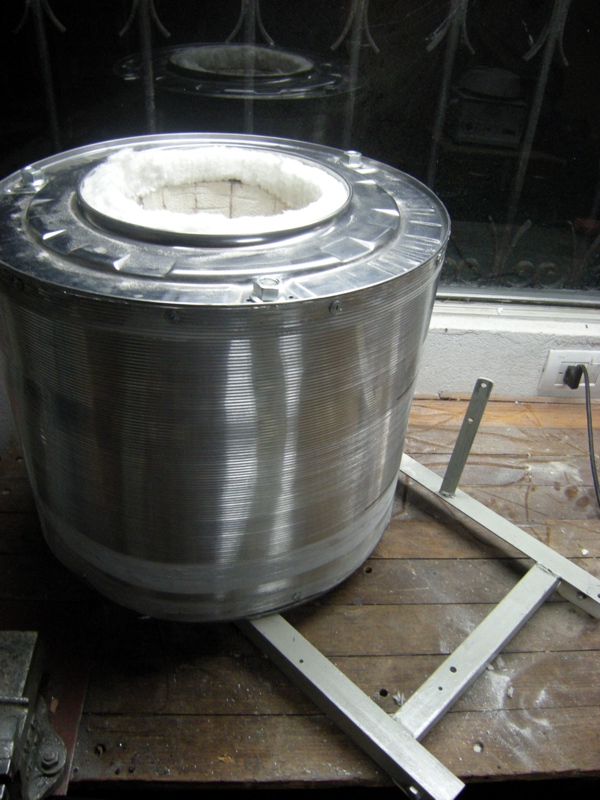 |
Fig nº 7.- Séptimo
paso: Se hizo una base de hierro ángulo para ubicar todos los
componentes. Poner un ladrillo aislante para conducir la entrada de
la llama, una vuelta de manta cerámica de 2,5 cm y se retiene
todo con cinta de nicrom y un tornillo de acero AISI 304. También
en la parte de arriba puse una capa de manta cerámica (espesor
de 25 mm) y sobre ella le puse la tapa retenida con tres varillas
de 12 mm con los extremos roscados y con tuercas (todo cincado para
mejorar su resistencia a la corrosión). Como terminación
exterior le puse una vuelta de chapa de corrugada de aluminio y retenida
con tornillos autoperforantes. |
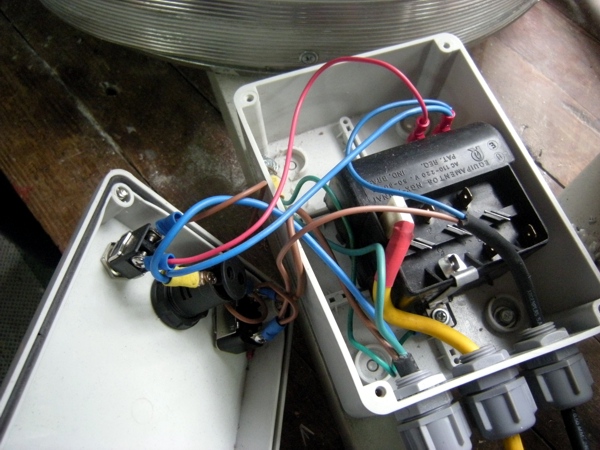 |
Fig nº
8.- Octavo paso: El control eléctrico se ubicó en una
caja plástica con una bobina de alta tensión (de las
usadas en las cocinas y en desuso por tener alguna salida quemada). |
 |
Fig
nº 8.- Octavo paso:Detalle del montaje del soplador/quemador
y de la parte eléctrica. |
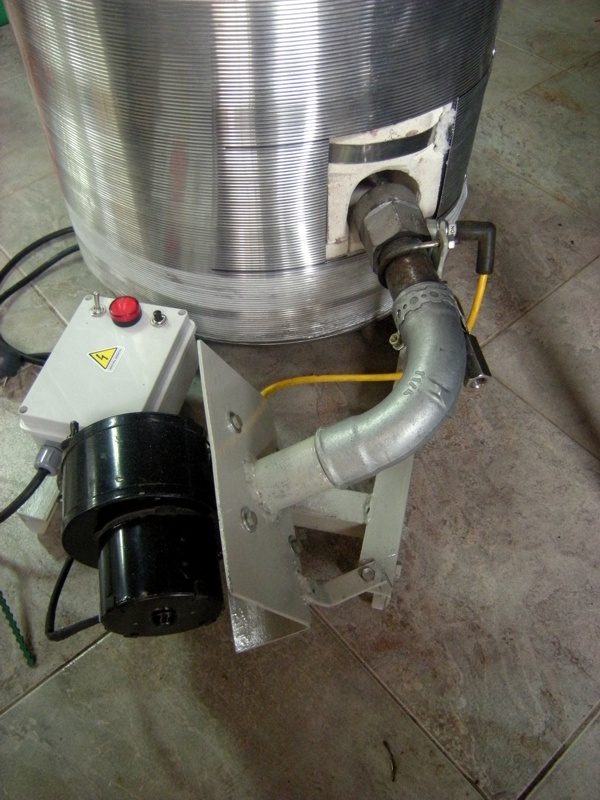 |
En la fig. nº 9 se observa el quemador propiamente dicho.
Consta de un ventilador centrífugo, una curva de fundición
sólo a los fines de tener un equipo mas compacto, un niple
corto y la boquilla del quemador propiamente dicho. Ahí se
le puso una bujía de auto para tener el encendido. Se uso
cable de silicona de alta tensión y temperatura (color amarillo),
un chupete de goma de uso automotor, una llave de paso de gas para
regular el caudal de gas.
Obsérvese la posición de la boquilla del quemador
(unos milímetros antes de la entrada) y la cinta de nicrom.
En la caja eléctrica se observa la llave de encendido, el
ojo de buey que indica la energización y el pulsador para
accionar el encendido.
Tanto el quemador, como la caja eléctrica son desmontables.
El uso de varillas roscada que sujetó el horno permite el
desmontaje del horno y ademas sujetar a futuro elementos como tapas,
termocuplas, etc. También facilita su desarme.
La base de hierro esta realizada con perfil ángulo de hierro
soldado y con unas patas de plástico de nylon.
|
Fig
nº 9- Vista lateral de la zona del quemador. |
|
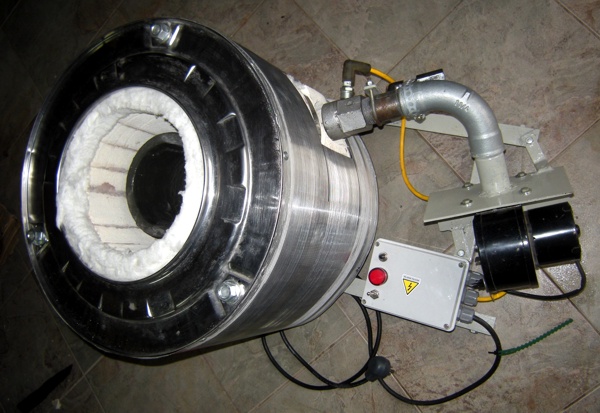 |
Fig
nº 10- Vista superior del horno terminado y con el crisol
dentro de la cámara del horno.. |
Bibliografía y fuentes de información
Internet: Se deja al lector la selección de la información
al nivel de aplicación que desee.
Para tener un panorama general de los hornos sugiero el texto "Hornos
Industriales" de W. Trinks y MH Mawhinney, tomos I y II. Es de Ediciones
Urmo. Tengo una edición vieja pero me sigue siendo muy útil.
|